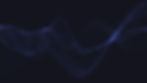
Understanding a Fluid's Condition State, in Real Time, Anytime, With Online Oil Condition Monitoring
Miniotec provides an advanced industrial IIoT fluid monitoring system through sensors capable of continuously monitoring oil temperature, oil quality, metallic wear debris and particulates in an asset’s lubrication system using in-line sensing technology for monitoring the health state of lubricating fluid.
​
Traditional oil sampling analysis is typically undertaken by analysing oil samples in accredited oil labs – a slow and costly process. With the real time monitoring sensors Miniotec offers, we now take the testing out of the lab and analyse equipment fluids continuously within a robust online monitoring system, without manual intervention – a significant operational advantage.
​
Online fluid / oil condition sensors are able to:
-
Provide remote monitoring, continuous real time insight and data analysis to validate oil health whilst the equipment is still in operation
​
-
Minimise repair costs or catastrophic failure through the early detection of changes and trends in an oil's condition properties
​
-
Measure several critical properties of the oil contamination and oil degradation, including relative humidity, wear debris and viscosity, responsible for the most common oil issues affecting plant equipment - all in real time
​
-
Reduce secondary damage and mechanical wear to an asset and its components due to mechanical faults
​
-
Maximise the operating life of the asset through delivering continuous data of a lubricant's health state to support advanced condition-based maintenance practices, including knowing how to better optimise fluid drain intervals
​


Automate a Manual Process with Real-Time Data Analysis


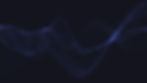
Changes to Fluid Quality and Wear Debris Typically Revolve Around Events
Collect Real Time Analytics
of Key Fluid Parameters
An Easy to Install Oil Monitoring Solution
" Oil Condition Monitoring Sensors that measure Fluid Quality and Wear Debris are extremely reliable and provide a layer of insurance that the equipment’s lubricating oils are being monitored 24/7 and not intermittently unlike traditional lab analysis condition monitoring "
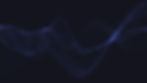
Important Benefits Of Online Oil Monitoring Systems and Real Time Fluid Analysis Sensors

Optimise machinery oil sample timing and maintenance intervals with real time data

An Online Oil Condition Sensor improves asset health state awareness and reliability

Advanced warning enables improved asset
maintenance and logistics planning

Identify contamination events. Observe changes to operating temperature.

Reduce operating costs of unscheduled downtime

Detect oil changes and top-up events within an oil circuit

Verify proper lubrication system maintenance

Track water contamination and moisture levels
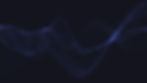
Support Your Knowledge of Online
Oil Condition Monitoring
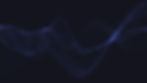
Where Fluid Sensors Play a Critical Role




Wind
Oil and Gas
Mining
Industrial Equipment

Marine

Water and Utilities

Rail and Locomotives

Manufacturing