The True Cost of Deferred Maintenance
- Miniotec - Intelligent Solutions
- Aug 23, 2022
- 6 min read
Updated: Mar 7, 2024
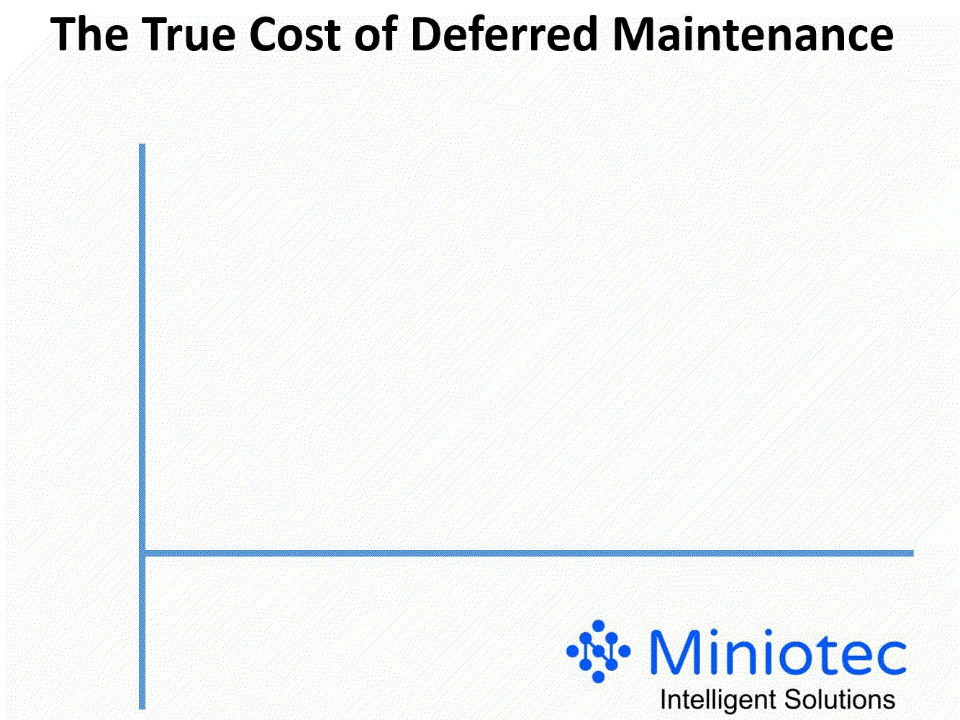
We are all aware that the longer we operate a machine or asset that requires repair or has been identified to be problematic, the more money it will cost to repair it. Engineers and technicians have long recognised that good maintenance practises are critical to cost-effective asset performance over the asset's useful life. But what is the true cost of this deferred maintenance?
When an organisation attempts to decrease their maintenance budgets by cutting maintenance spending, maintenance costs will only reduce until spending falls below the machines' minimum needs.
If maintenance spending falls below the bare minimum needed for the asset to operate as intended and assets are run to failure, the outcomes will be an exponential cost increase that invariably will be inversely proportional to the anticipated savings.

Introducing the Inverse-Square Rule for Deferred Maintenance
Continuing the above setting, when a part within an asset is identified to be failing but is operated to failure (OTF), the resultant cost required by the organisation to overcome the breakdown event will invariably be approximate to the square of the cost of the central failure part.
If the breakdown event worsens, the energy needed to recover from the breakdown occurrence will continue to square with each successive level of failure.
The above is outlined in an interesting philosophy noted by The Geaslin Group in their paper “Geaslin’s Inverse-Square Rule for Deferred Maintenance Effort”. Within their paper they note:
“If a part is known to be failing but left in service until the next level of failure, the resultant expense will be the square of the primary failure part."

So What Is The True Cost Of Maintenance For A Typical Example?
If we use the example of a $100 electric motor bearing that is known to be failing but repairs are postponed until the rotor fails and damages the stator, the rewind cost can be considered as the square of the bearing or $10,000. If that bearing could have been changed for $650 in early intervention activities (the first sign the bearing was known to be defective), delaying this work order has a risk/reward ratio of more than 15:1 in direct maintenance costs.
If we include lost production costs of five (5) hours and $4,000 per hour, the risk/reward ratio increases to almost 50:1.
What if the scenario is actually more onerous, for example, if we include constraints such as remoteness of the facility limiting repair, lack of spare parts because of supply constraints, failure of the part during a period of limited site attendance, production opportunity losses etc. then all or one of these events could amount to exponential production revenue losses and the risk/reward ratio would be significantly more.

The above scenario is an interesting anecdotal example of the true cost of deferred maintenance and provided as a general guide but when you consider this in practice, the fundamental elements appear to hold true. It is not necessary for the scenario to be validated precisely. The scenario provides practical and credible support of the fact that if maintenance costs are not applied proactively early, such as within predictive maintenance strategies, the outcomes can be significantly increased costs for asset owners of their equipment.
YOUR ACTION: Evaluate the same philosophy with your own examples but remember to include all credible user cost savings, not solely the cost of the original part failure and its repair.
How Can Digital Transformation through IIoT Support?
When IIoT solutions are adopted within a Predictive Maintenance framework, maintenance processes are supported with greater efficiencies and awareness that promotes better maintenance.
When we consider the main causes of deferred maintenance tasks, it is quite clear where IIoT brings benefits.
1. Time
IIoT enables the Engineer or technician to shift away from routine tasks to more strategic and proactive analysis of data and root cause analysis. Timely and relevant prescriptive data equals the ability for more timely decisions to be made.
2. Budget
The breadth of performance information gained through IIoT collected data enables asset maintainers to shift their focus from risk avoidance processes to prescriptive maintenance activities which is a strategy that has been proven to reduce maintenance costs by 40-60%.

3. Visibility
The consistency and breadth of data IIoT sensors collect, coupled with automated analytical evaluation, supports making fault classification easier.
Whether it is vibration analysis defining a type of defect and thus the type of failure mode likely to be experienced or oil sensors that provide real time water concentrations within a lube circuit, or sensors on piping networks detecting relative humidity to support identifying corrosion under insulation issues, IIoT sensors will transform the visibility of assets and enable better and more timely decisions to be made.
4. Spares
IIoT devices and the powerful analytics that underpin the solution, can determine faults very early after a fault event is initiated and advise how the equipment is likely to fail. This early detection of a failure provides time to plan and schedule for replacement parts or restoration of a failing part or asset with the aim of mitigating interruptions to operations and production.
5. Labour
As IIoT solutions enable the move from reactive maintenance to more proactive and holistic efficient strategies, the smallest of problems can be identified very early in the failure cycle, well before manual processes can typically identify them. Accordingly, IIoT solutions support automated monitoring and analytics that liberates an existing maintenance team’s available time, enabling additional capacity to perform more proactive and valuable work that will mitigate deferred maintenance risks.
6. Skills
If maintenance jobs develop that exceed a maintenance team's credentials, specialisation or experience, the job will invariably be added to the deferred maintenance task list until the business has the resources to outsource the issue.
Elevate your asset management and optimise your operations: take our online IIoT opportunity evaluation today for actionable insights.
The best IIoT solutions available today, such as those provided by Miniotec, provide automated prescriptive analysis and commentary that specifically highlight not only the likely fault detected, but also provide indicative activities that can be taken to resolve the issue or, at the very least, provide timely guidance as to the severity of the fault identified to enable prioritisation of maintenance actions to be taken. Again, giving the engineer or technician more information into how to use available budgets and time while reducing the possibility of deferring maintenance actions in the first place.
Achieving Safe and Dependable Operations is Crucial to an Organisation's Success.
Unplanned downtime, especially the loss of production availability, is one of the primary causes of decreased profitability, not to mention safety and compliance risk.
While deferring maintenance may save maintenance budgets in the short term, it presents a serious and unneeded risk that is demonstrated to increase the prospect of downtime that organisations can and should avoid. Effectively, reduce deferred maintenance else anticipate your maintenance costs will increase considerably....unexpectedly.
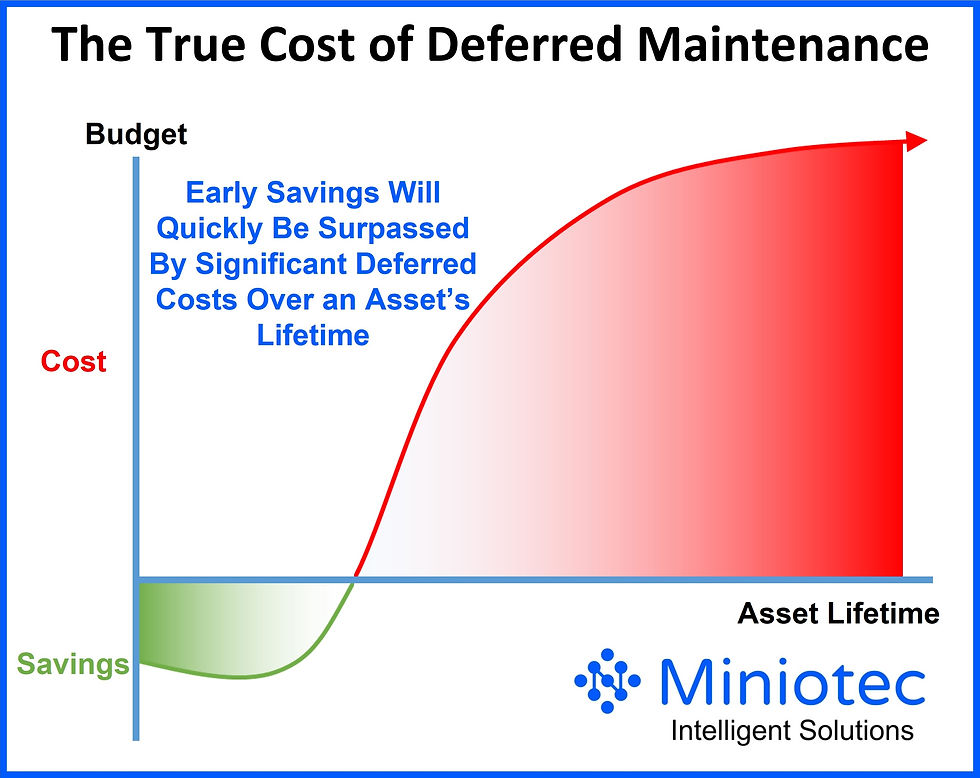
"Moving away from a cycle of having a deferred maintenance backlog is similar to the analogy of moving out of debt. Maintenance activities in your backlog add up over time, much like compound interest on a debt."
Adopting IIoT solutions is a critical component and undervalued enabler of Digital Transformation that, when combined with the appropriate predictive maintenance framework involving People and efficient Processes, will support better maintenance practises, including the reduction of deferred maintenance.
Let us know your thoughts?
We are eager to understand your Digital Maintenance focus and where we could support.
This article was written on behalf of Miniotec by Tony Nitchov. (connect on LinkedIn).
Best;
info@miniotec.com
About Miniotec:
Miniotec is a digital consulting and technology solutions provider, dedicated to supporting companies in their digital transformation journeys. Established by a group of experienced engineers, we emphasise the harmonious integration of people, processes and technology. Our team has a rich history of working across various sectors, from energy and resources to infrastructure and industry. We are trusted by the world's largest miners, oil and gas giants, utility companies and even budding start-ups and believe in the transformative power of the Industrial Internet of Things (IIoT) and its role in unlocking valuable data insights. Through IIoT, we aim to facilitate better decision-making, enhance operational activities and promote safer work environments. At Miniotec, our goal is to guide and support, ensuring every digital step is a step forward.
digital maintenance
big data and analytics
future trends
predictive maintenance