Uncovering the Power of Fluid Analysis: Using Advanced Online Oil Condition Monitoring Sensors
- Miniotec - Intelligent Solutions
- Feb 4, 2023
- 12 min read
Updated: Mar 15, 2024
Online Oil Sensors = Continuous Fluid Insight to Optimise Machine Health

The Current State of Play
In the evolving landscape of industrial asset management and machinery maintenance, leveraging technology for real-time monitoring of oil and other crucial fluids becomes indispensable. Industries ranging from petrochemicals to renewable energy, and from construction to maritime operations, are increasingly seeking efficient, reliable oil condition monitoring systems. Traditional oil analysis, conducted via periodic laboratory sampling, while useful, presents challenges including delays, high costs, and sporadic insights into fluid health. The advent of Industrial Internet of Things (IIoT) and sensor technologies, complemented by sophisticated analytics, now offers the possibility to monitor fluid conditions continuously, in real-time, enhancing decision-making for asset managers.
Miniotec provides a cutting-edge industrial IIoT fluid monitoring solution that utilises fluid quality sensors, wear debris sensors and other sensors to continuously monitor parameters such as metallic wear debris and particulates in an asset's lubrication system, in addition to in-line sensing technology for monitoring the health state of lubricating fluid. With these solutions, Miniotec can provide asset managers with real-time insight into the health of their equipment's oil, allowing them to minimise repair costs, reduce secondary damage due to mechanical faults and maximise the operating life of their assets.
Traditional Monitoring of Lubricant Health - Limitations
Traditional oil analysis and monitoring of lubricant health involves collecting a sample of oil from a machine or system and sending it to a laboratory for testing and analysis. This process involves multiple steps, including:

Sample Preparation
Physical Tests
Chemical Tests
Wear Debris Analysis
Spectrographic Analysis
Ferrographic Analysis
Interpretation of Results
Reporting
Despite its reliability, this method faces limitations: it is time-consuming, susceptible to human error and its effectiveness hinges on the quality of sample collection - akin to finding a 'needle in a haystack'. Furthermore, the inherent delays—from collection to analysis—often mean that actionable insights are available only after significant delays, a luxury that fast-paced industrial operations can seldom afford. In addition, traditional oil analysis can be very expensive, especially for large industrial operations with multiple machines and systems or assets in remote locations.
In contrast, the advantages of IIoT in fluid analysis through online oil condition monitoring, with its real-time data acquisition, offers a more dynamic, cost-effective solution.
The process of traditional oil analysis and monitoring is typically slow and can take anywhere from 10 - 28 days from oil sample collection to findings.
It is also important to note that changes in fluid quality and wear debris typically revolve around events. For example, changes in temperature can cause an increase in viscosity, which can affect the flow of oil to moving parts and cause increased friction and wear. This is why laboratory analysis can have considerable limitations and why fluid quality and wear debris sensors are playing a very critical and important role in monitoring the health state of equipment and optimising machinery efficiency.
Benefits of Real-Time Fluid Analysis
The adoption of real-time fluid analysis via online oil condition monitoring sensors marks a transformative shift in equipment maintenance. By providing instant insights into the health of lubricating oils, these technologies enable a proactive maintenance approach. Key benefits include significant cost savings through early detection of potential issues, extended equipment lifespans and optimised maintenance schedules. This approach not only reduces the likelihood of mechanical failures but also supports a strategy of condition-based maintenance, resulting in a more efficient allocation of resources and improved operational uptime.

Whilst not trying to duplicate laboratory derived results, by providing real time analysis whilst the equipment is still operational, Miniotec can continuously monitor fluid performance and wear debris generation.
Oil sensors are able to measure several critical properties within an oil stream that are responsible for the most common issues that affect plant equipment and can cause secondary damage to assets. By continuously monitoring these properties, online fluid condition sensors can detect changes in the oil quality and enable asset owners the ability to make more informed decisions and take more timely actions to prevent costly secondary damage.
Moreover, real-time oil condition monitoring for industrial machinery measures several critical properties of the lubricating oil, including relative humidity and wear debris, which are responsible for the most common oil-related issues affecting plant equipment. By measuring these properties, equipment owners can take proactive measures to prevent secondary damage to their assets and reduce unscheduled downtime.
Continuous Monitoring for Optimal Asset Health

Continuous, 24/7 monitoring of oil and fluid health is pivotal for the longevity and efficiency of industrial assets. With the sensor technologies Miniotec offer, asset owners are empowered with an online monitoring system that alerts them to any irregularities in real time.
Fluid quality and wear debris sensors provide a layer of insurance that the equipment's oil is being monitored continuously and not just intermittently, as is the case with traditional laboratory analysis. This continuous oversight ensures that mechanical wear, moisture intrusion, temperature fluctuations and oil degradation are promptly addressed, facilitating preemptive maintenance actions. By seamlessly integrating with existing asset management systems, these sensors not only safeguard against unexpected downtime but also pave the way for a more informed, data-driven approach to asset maintenance and management.
Oil Condition Monitoring: 'Best-In-Class' Sensor Technology
The online oil monitoring solution Miniotec offers include the worlds most advanced sensors of its service and are 'best-in-class' for monitoring the health state of lubricating fluids and capable of replacing most periodic (preventative) oil sampling requirements.
The sensors are able to continuously monitor metallic wear debris and particulates in an asset's lubrication system, in addition to in-line sensing technology for monitoring the health state of lubricating fluid.
The Sensors Provide Analysis from the Same Oil Stream Within a Self-Contained Ruggedised Box
For example, the fluid quality sensor provides continuous insight to oil health, promoting condition-based maintenance practices such as optimised fluid drain intervals and reduced dependence on offline analysis. This solution uses Electrochemical Impedance Spectroscopy (EIS), a sensing method based on analysing a fluid's electrical properties across a range of frequencies to determine its condition. EIS is used to track changes in the impedance over time and is thus able to collect more information than other single-frequency dielectric or conductance sensors in the market.
The benefits of EIS include:
Different frequencies correlate more closely with the various actual condition indicators within an oil circuit.
The EIS solution utilised in the Oil Sensor is superior to competition sensors which only perform single frequency analysis
These sensors can detect most, if not all, key oil events and project remaining useful life of the oil while the asset is in operation.
While these sensors cannot exactly duplicate lab analysis results, they can provide the necessary and more timely insight to make maintenance decisions well before damage occurs remotely, in harsh conditions and hazardous environments.
The analytics dashboard reports provided as part of the monitoring system immediately notifies you when it detects something to be concerned with, so you can investigate and resolve the root cause as soon as possible to prevent costly secondary damage or catastrophic failure. With advanced warning and real-time insights, it enables improved asset maintenance and logistics planning, verifies proper lubrication system maintenance, identifies contamination events, tracks water contamination levels and optimises machinery oil sample timing and maintenance intervals. Furthermore, this data can reduce operations and maintenance costs by optimising your maintenance and oil change schedule.
Adopting online oil quality sensors is a key enabler to shifting the oil sampling paradigm from periodic to true ‘real-time’ condition-based monitoring whilst the equipment is still online and operational. Best in class reliability programs have found a step change in asset longevity and performance by implementing online fluid sensor in their oil monitoring programs.
Key Industries and Applications
The more modern industrial IIoT fluid monitoring systems are suitable for a wide range of industries and applications. The system is critical in industries such as wind power, oil and gas, mining and marine, where reliable and continuous monitoring of oil and other fluids is essential. The system is also suitable for industries such as rail and locomotives, manufacturing, water and utilities and other industrial equipment, where efficient and cost-effective maintenance practices are vital.
The Justifications for Traditional Laboratory Oil Analysis and/or Arguments Against Online Oil Analysis Sensors
Oil analysis is an essential tool for predictive maintenance, but there is a growing debate between traditional oil analysis undertaken in a laboratory and the use of online oil sensors.
While some parties remain steadfast against the use of online sensors, the truth is that there is a place for both approaches. Traditional oil analysis provides detailed information, though providing only intermittent insight, but has been a trusted method for many years. However, with the advancements in technology, online oil sensors are proving to be a valuable asset in providing real-time data and more consistent analysis. Below we have explored some of the arguments against online oil sensors in fluid condition monitoring and why online oil analysis will continue to prove more value in the future.
Argument 1: Online Oil Sensors only measure a single or a few parameters, which is not enough for an accurate assessment of fluid condition monitoring.
While it is true that some online fluid sensors may only measure one or a few parameters, advanced sensors can measure multiple parameters that are crucial to determining the oil condition. This makes them more effective in detecting irregularities and reducing damage.
The sensors can be used to supplement the traditional laboratory analysis, which provides a snapshot of the past, by providing real-time data on the oil's present and most recent condition. This helps maintenance personnel to be more sensitive to oil changes every day in real-time, not every 3-6 months or longer.
Argument 2: Online Oil Sensor data does not correlate with conventional laboratory data and do not have absolute limits for interpretation.
The lack of correlation between the sensor output and laboratory data is a matter of compatibility and not a limitation of the sensors themselves. Also, the quality of sample collection determines the quality of the analysis.
Online oil monitoring can provide data on the gradual decline of oil quality over time, enabling the detection of warning signs and critical limits. It also supports understanding of the remaining usable life (RUL) of the oil and quickly identifies any instances of contamination. With the help of online oil quality sensors, trending elements like soot levels, base number, relative humidity and the depletion of additives can be readily monitored and analysed.
The results of the sensors can be interpreted in the context of a broader range of information, including historical trends, usage patterns and other factors.
Argument 3: Online Oil Sensors are not cost-effective and usually have a high purchase price.
The long-term cost savings from using online sensors, such as reduced downtime and maintenance costs, outweigh the initial cost and when considered against the value they return, can be considered low cost.
The ability to continuously monitor the fluid conditions in real-time provides valuable insights that is not be possible with traditional methods..
Argument 4: The informative value from online oil sensors is limited to one type of oil or a specific unit.
This is not a universal limitation of all online fluid sensors analysing lubricating oils. Advanced models can be adapted to work with different types of oil and machinery, making them more versatile and useful and capable of identifying potential catastrophic failure mechanisms.
By measuring multiple parameters, such as the sensors Miniotec offer, the detection capabilities the sensors provide will enable a more comprehensive understanding of the oil's condition and its impact on the machinery.
Argument 5: Conductivity sensors are not sufficient to describe oil condition with sufficient accuracy.
This is a limitation of specific types of sensors and not all online fluid sensors. Advanced models can use multiple sensors and measurement techniques to provide a more accurate assessment of the oil condition.
Conductivity sensors can still provide valuable information, especially when considered over long-term use and in combination with other sensors.
Argument 6: Viscosity is not enough to assess oil quality or usability.
This is a limitation of using only viscosity as a parameter and not a limitation of online fluid sensors themselves.
By measuring multiple parameters, including viscosity, modern online oil sensors can provide a more comprehensive understanding of the oil's condition and its impact on the machinery.
Argument 7: The accuracy of online sensors may be affected by environmental factors.
Advanced online sensors are designed with measures to mitigate environmental effects and maintain accuracy.
The ability to continuously monitor the fluid conditions in real-time provides valuable insights that is not be possible with traditional methods using periodic laboratory oil analysis.
Argument 8: The installation of online sensors may be difficult and time-consuming.
Many online fluid sensors have user-friendly installation procedures and the installation process is often less time-consuming than traditional methods of oil sampling and regularly waiting for equipment to be taken offline.
The long-term benefits of online sensors, such as reduced downtime and maintenance costs, outweigh the initial installation effort.
Argument 9: The data collected by online sensors may not be reliable or trustworthy.
Advanced online sensors, like those offered by Miniotec, are designed with the highest measures of quality to maintain accuracy and reliability. Also, the quality of the sample collection taken for traditional laboratory analysis determines the quality of the analysis and this is sometimes an inherent issue and negative constraint regarding the reliability of results from traditional approaches.
The real-time monitoring capability of online sensors provides a continuous stream of data that can be verified against traditional methods (if required).
Argument 10: There may be compatibility issues between the online sensors and existing equipment.
Many online sensors are designed with compatibility in mind and can easily integrate with existing equipment and or client historians.
The ability to continuously monitor the fluid conditions in real-time provides valuable insights that may is not possible with traditional methods.
Online Oil Sensors and their Benefits to Renewable Wind Energy
A 5-point summary of how the Online Oil Sensors Miniotec offer are improving the maintenance and operational performance of wind turbines in the renewable industry.
1. Monitoring Gearbox Health:
Identifying signs of gearbox wear, metal debris or contamination, enabling early detection of potential problems and reducing downtime for maintenance.
2. Lubricant Condition Monitoring:
Monitoring the condition of lubricating oil to offer insights into the health of the fluid circuit. Changes in the oil's physical and chemical properties, such as an increase in viscosity or metal wear debris, have invariably indicated issues that needed attention.
3. Cost Savings:
Reductions in unscheduled maintenance by knowing where the turbine ‘bad actors’ are. Furthermore, analysis of lubricant data continues to improve decisions on oil changes, helping to optimise lubricant use and reduce costs.
4. Improved Understanding of Wind Turbine Operations:
Online oil analysis is providing detailed information about the operating conditions of wind turbines, including temperatures, loads and wear patterns. This information is being used to optimise turbine performance and improve their overall efficiency.
5. Better Maintenance Planning:
Technicians are improving maintenance practices by identifying when and where maintenance is most necessary in their windfarm at the most optimal time by monitoring the state of each turbine's lubricating oil. Online oil analysis is significantly enhancing a windfarm owner's knowledge of which turbines are most critical in their asset group and adapting their maintenance strategy as required to ensure the good turbines are kept good, especially given that most wind farms have well over 50 turbines. This is in contrast to a systematic approach to preventative maintenance scheduling, priority ranking and performance monitoring.
Integrating Combined Online Oil Analysis and Wireless Vibration Sensor Technology in your Maintenance Strategy
Both vibration analysis and oil analysis are vital instruments to have in your maintenance toolbox when it comes to evaluating the status of assets and diagnosing potential problems. These methods can sometimes be used in conjunction to diagnose issues such as pinion tooth wear or failed bearing lubrication. To find problems like unbalance and misalignment however, there are instances when only vibration analysis will work. Additionally, oil analysis is the only method for detecting water in oil.
Using IIoT sensors for vibration analysis and online oil analysis can also improve the accuracy of the data collected. By collecting data in real-time, engineers and condition monitoring technicians can have assurance that the information is accurate and up-to-date. This helps to avoid any potential errors that could occur if the data was collected manually. Both methods are necessary for any successful maintenance programme, but if you include a strategy of combining them, you may obtain a more thorough understanding of the asset's health status.
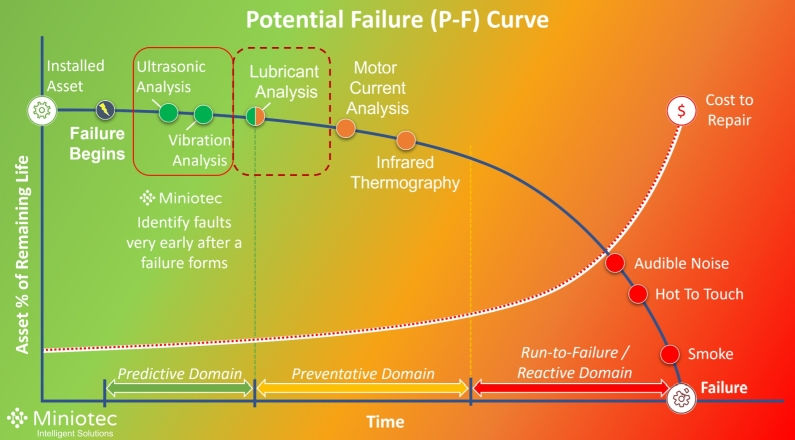
Case Study - Combining Oil Analysis and Vibration Analysis for Predictive Maintenance
In the primary plant of a particular Client, a significant proportion of the rotating machinery are installed in outside conditions with minimal protection from the elements. Due to the two contrasting seasons that the climate offers at this plant location — a tropical summer and a mild winter — these assets are susceptible to external contamination if their seals are ineffective or to accelerated environmental wear. To protect the machinery as best as possible and prevent unplanned downtime, the maintenance team decided to leverage online oil sensors and wireless vibration sensors to monitor the health of their equipment.
Post installation, oil analysis and vibration analysis were key in detecting potential issues within a planetary gearbox. The online oil analysis results showed a drastic increase in iron content by almost 10x pointing to bearing wear. Meanwhile, vibration analysis confirmed the bearing deterioration, with values still within acceptable limits but with a rising trend as indicated by the trend curve. This combination of results, with high severity, highlighted the need for immediate intervention.
With the information gathered from both sensors, the plant personnel were able to replace the equipment's oil and impacted bearing. During the maintenance review process, the oil and bearing were assessed by the technical team which validated the sensors were correct in their diagnosis. This success mitigated an unplanned breakdown and reduced energy consumption.
By combining oil analysis and vibration analysis, the plant has been able to achieve an effective maintenance program that monitors the health of their assets. These techniques have proven to be indispensable in their everyday maintenance program, providing an earlier warning of potential failures and aligning interventions with production planning. The result is balanced equipment with reduced vibration, longer-lasting components and an overall increase in productivity.
In Summary
Oil monitoring systems have come a long way from traditional oil analysis methods.
With the advent of advanced sensors and real-time fluid analysis technology, we are now able to gain a comprehensive understanding of a fluid's condition health state in real-time, without manual intervention and while the equipment is still in operation.
Fluid sensors, like those offered by Miniotec, play an important role in various industries, from monitoring the condition of oil and gas equipment, to ensuring the safety of heavy vehicles and even detecting potential problems on ships and locomotives. These sensors can detect changes in fluid properties such as oil temperature, water content through relative humidity, particle sizes, oxidation stability, oil contamination (e.g. additive content), viscosity and numerous other parameters, providing valuable information for maintenance and operation personnel.
By detecting potential problems early, online fluid sensors can help prevent costly downtime and ensure that equipment is running smoothly. The use of online fluid sensors is thus essential for optimising performance, increasing efficiency and ultimately reducing costs in various industries.
If you have not considered online oil sensors thus far in your maintenance strategies, you should consider them in the future - they can make a significant difference to the uptime of your equipment.
Stay safe.
Let us know your thoughts?
Best;
digital maintenance
online oil analysis
fluid condition monitoring
digital acceleration
digital transformation
wireless vibration
miniotec